heavy duty trolley wheels
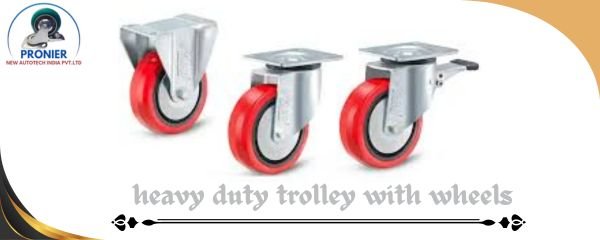
In the world of industrial and commercial transportation, heavy-duty trolley wheels play a pivotal role in ensuring efficient and safe movement of goods. From manufacturing plants to warehouses, airports to hospitals, heavy-duty trolley wheels bear the weight of commerce, enabling the seamless flow of materials and products. Over the years, these wheels have undergone significant evolution, driven by advancements in materials, engineering, and design. In this article, we delve into the evolution of heavy-duty trolley wheels, exploring the key factors influencing their design, performance, and applications.
The Evolution of Materials
Historically, heavy-duty trolley wheels were predominantly made of cast iron or steel. While these materials provided durability and strength, they also came with drawbacks such as high weight and susceptibility to corrosion. However, with the advent of modern materials science, manufacturers began experimenting with alternative materials such as polymers, composites, and advanced alloys.
Polyurethane emerged as a game-changer in the world of heavy-duty trolley wheels. Its exceptional resistance to abrasion, chemicals, and impact, coupled with a relatively low weight, made it an ideal choice for demanding applications. Polyurethane wheels offered improved traction, reduced noise, and enhanced maneuverability, setting a new standard for performance in industrial environments.
The Rise of Ergonomic Design
In addition to material advancements, the design of heavy-duty trolley wheels underwent significant evolution to address ergonomic concerns. Ergonomics became a critical consideration as industries recognized the importance of reducing strain on workers and optimizing efficiency. As a result, heavy-duty trolley wheels evolved to feature ergonomic designs such as ergonomic handles, adjustable heights, and swivel capabilities.
Swivel casters, in particular, revolutionized the maneuverability of heavy-duty trolleys, allowing them to navigate tight spaces and corners with ease. This innovation not only improved productivity but also reduced the risk of workplace injuries associated with manual handling.
Specialized Applications and Customization
As industries became more diverse and specialized, the demand for heavy-duty trolley wheels tailored to specific applications grew. Manufacturers responded by offering a wide range of customization options, allowing customers to select wheels optimized for their unique requirements.
For example, industries operating in corrosive environments, such as food processing or chemical manufacturing, benefited from wheels with corrosion-resistant coatings or stainless steel components. Similarly, sectors requiring strict hygiene standards, such as healthcare or pharmaceuticals, favored wheels with antimicrobial properties to prevent bacterial growth.
Furthermore, advancements in technology, such as 3D printing, enabled rapid prototyping and customization of heavy-duty trolley wheels. This flexibility empowered manufacturers to collaborate closely with customers to develop bespoke solutions that address their exact needs, whether it be load capacity, floor surface compatibility, or environmental conditions.
Looking Ahead
As we look to the future, the evolution of heavy-duty trolley wheels shows no signs of slowing down. Emerging technologies such as IoT (Internet of Things) and automation are poised to transform the landscape of industrial transportation, introducing concepts such as autonomous mobile robots and smart trolley systems.